|
 |
|
 |
|
|
|
Corrosion

HYCOOL Global Ltd will not accept responsibility for any damage that may occur should the product be used incorrectly.
No leaks - no corrosion
It is the contractors' responsibility to ensure that all service, installation and maintenance engineers are made familiar with the manufacturer’s, guidelines regarding the safe handling and correct use of HYCOOL® heat transfer fluids.
Wet corrosion
Problems with corrosion in indirect cooling systems have, in some cases, been explained simply by blaming the refrigerant for causing corrosion.
In many cases it is true that lack of knowledge about how corrosion arises, or about which type of corrosion actually exists, is the real problem. Here we will describe corrosion problems that, in simple terms, can arise in indirect cooling systems with circulating water-based refrigerants.
|
|
|
|
|
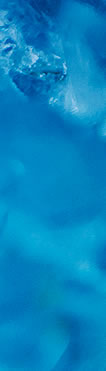 |
|
 |
 |
Some of the most common types of corrosion are:
General corrosion
In principle, this is a uniform decomposition of the entire metal surface.
Erosion corrosion
This is an abrasive effect that arises when the liquid contains abrasive particles like welding slag, sand, dirt or corrosive products. The oxide layer is formed when metal is worn away and the pure metal is exposed to oxygen. High velocity of liquid moving through the system may also contribute to this type of corrosion (turbulence corrosion).
Crevice corrosion
This type of corrosion occurs where the liquid is standing dormant in a small space or in a fissure between two components. The character of the liquid in the fissure or crevice is altered and an electrochemical cell is formed. The risk of corrosion will increase if the environment around the fissure is oxygenic.
Galvanic corrosion
This type of corrosion occurs where two metals of different nobility are bound together. |
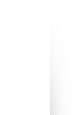 |
|
|
|
 |
|
 |
|
|